How can a textile factory identify a significant product defect, resolve it within two months, and improve the quality by 20%?
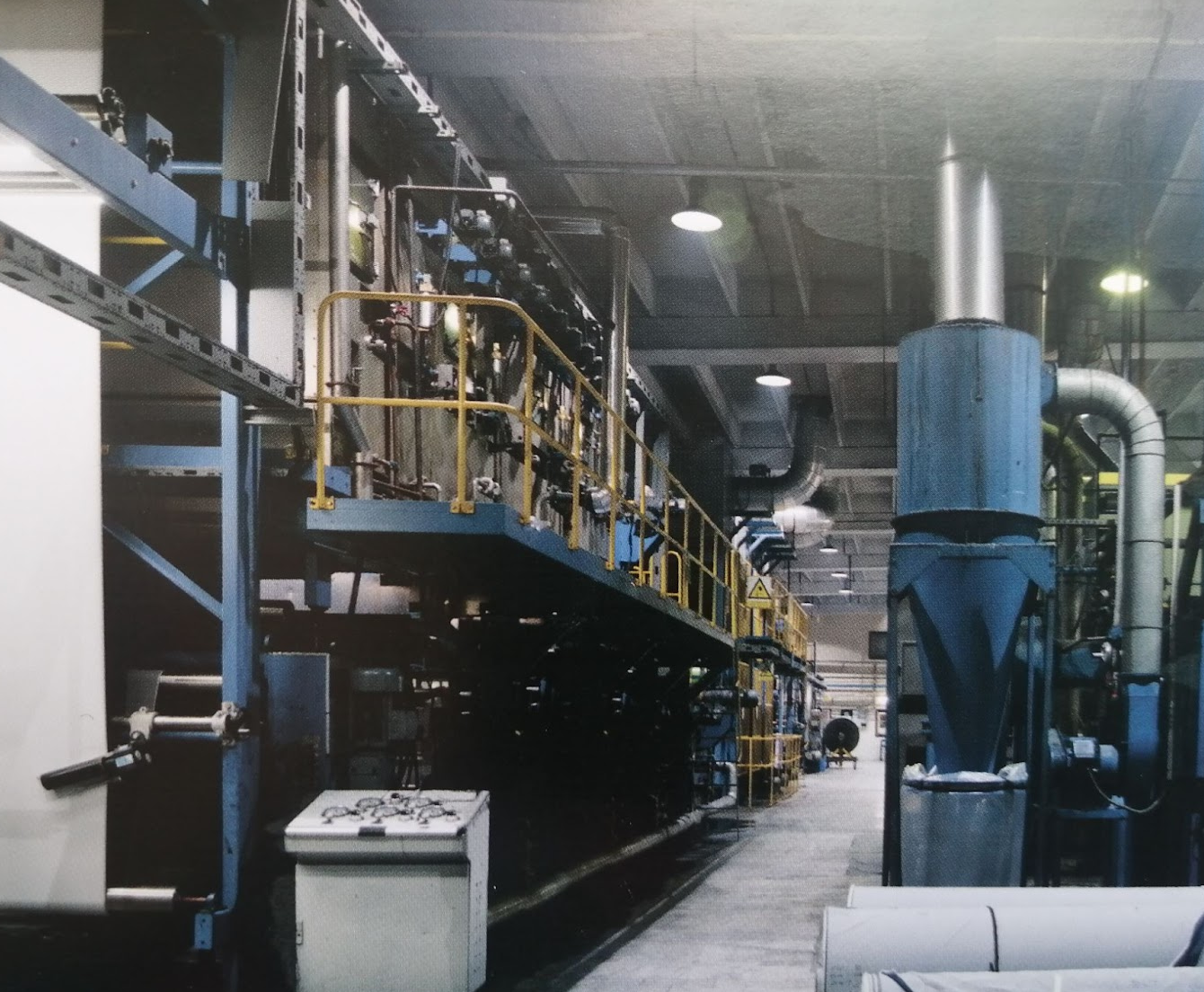
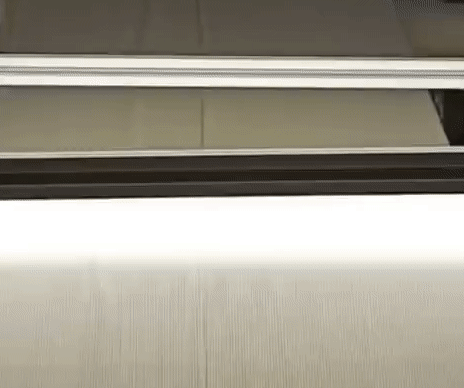
In the world of fabric production, defects in final products have plagued manufacturers since time immemorial. In this article, we will explore how one jean fabric producer successfully tackled a major defect by implementing FabriQC and Monitait services. By strategically installing these technologies in their production line, they not only detected issues but also uncovered the root cause behind a critical defect.
Identifying the Problem:
- Installation of FabriQC at the end of the Stenter machine.
- Observation of numerous defects, with one major issue standing out.
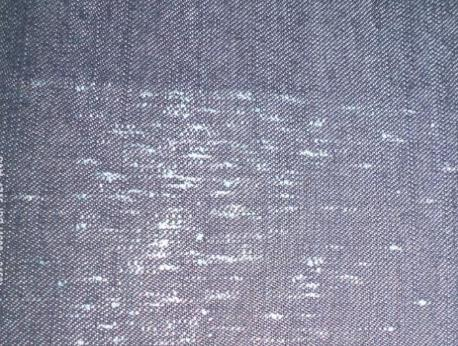
Utilizing Monitait Services:
- Implementation of Monitait in the production line.
- Discovery of a consistent pattern between cylinder temperature and the occurrence of the defect.
Analyzing Data and Quality Issues:
- Merging data from FabriQC and Monitait.
- Recognizing a correlation between malfunctioning pressure valves and the recurring defect.
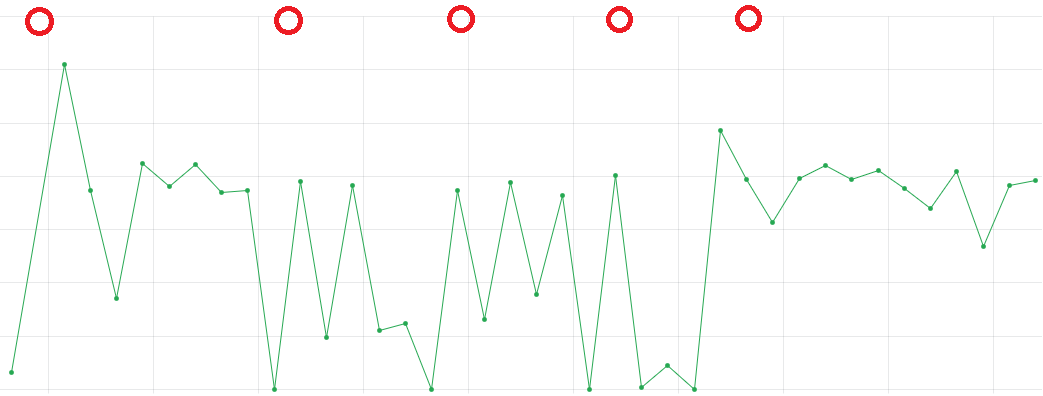
Resolving the Issue:
- Taking proactive measures to rectify the problem.
- Replacement of the malfunctioning pressure valves.
- Ensuring the defect is eliminated for future production runs.
The Importance of Root Cause Analysis:
- Emphasizing the significance of identifying root causes.
- Highlighting the relationship between final product quality and the production line's initial stages.
Conclusion

This case study demonstrates the critical role of advanced monitoring technologies like FabriQC and Monitait in addressing defects in fabric production. By not only identifying issues but also delving into their root causes, manufacturers can ensure higher-quality products and more efficient processes. In the ever-evolving textile industry, proactive problem-solving is essential to meet and exceed customer expectations.