How a Tire manufacturer prevents two days of downtime, and saves $200k annually
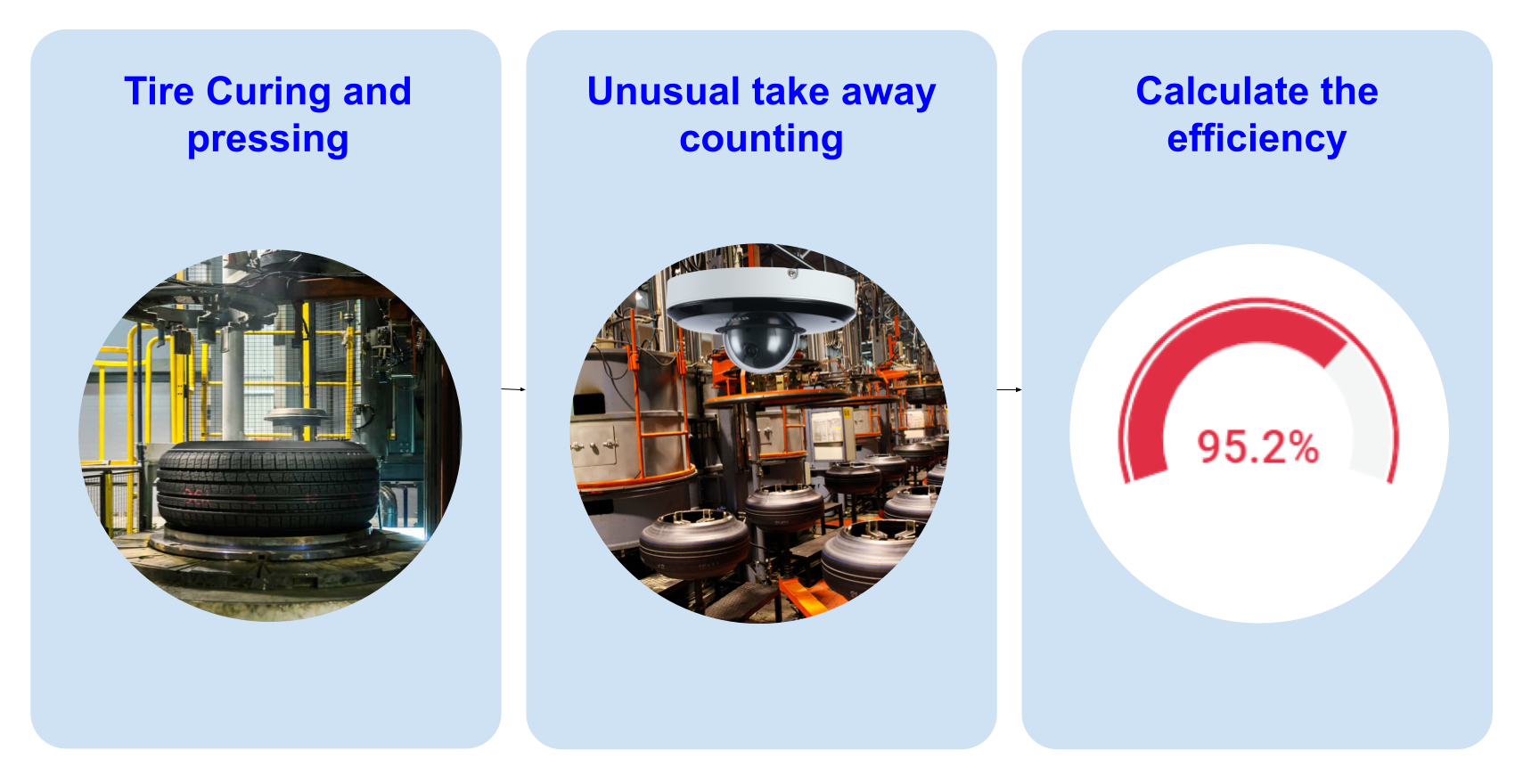
In the complex manufacturing world, efficiently managing raw material inventory while ensuring uninterrupted production is a constant challenge. For one company, the quest to strike the right balance between inventory cost and production capacity led to a game-changing solution
The Inventory Conundrum: Like many manufacturing companies, this company's commercial department used historical data, sales reports, and PLC counter readings to forecast their raw material orders for the next production period. Their goal was clear: minimize inventory costs while meeting production demands. However, as they soon discovered, relying solely on these methods had its drawbacks.
The Downtime Dilemma: At the end of one year, the company faced an unexpected challenge—a shortage of raw materials. This shortage resulted in a two-day production downtime, causing significant disruptions and financial losses. Faced with this dilemma, the company had two choices: stockpile more raw material as a safety net or dig deeper to understand the root cause of the shortage.
Opting for the latter, the company implemented Monitait, an intelligent monitoring service, to gain a deeper insight into their production process. They knew that to prevent future shortages, they needed to get to the heart of the issue.
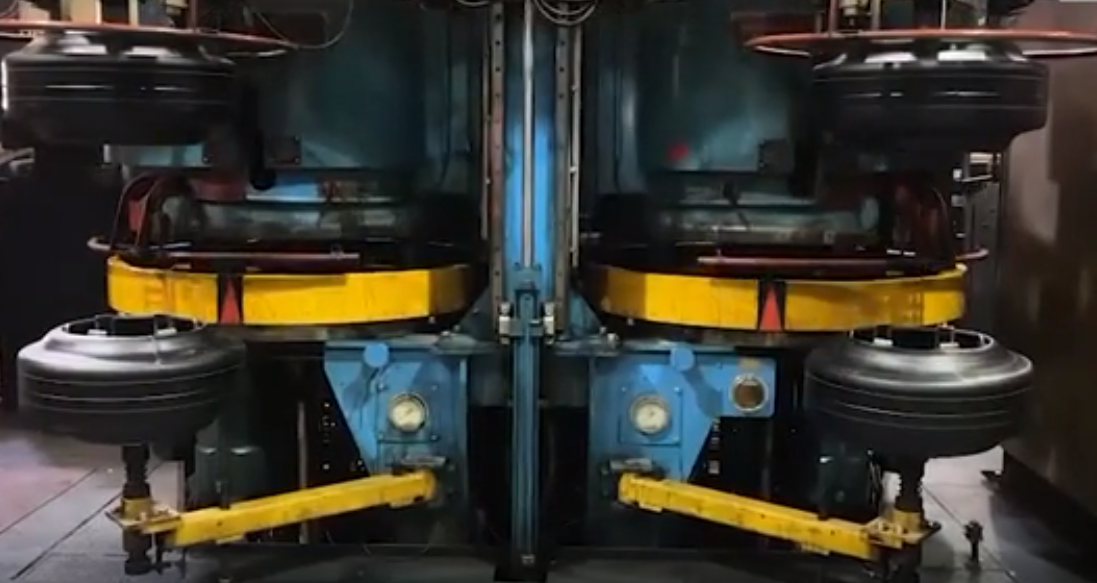
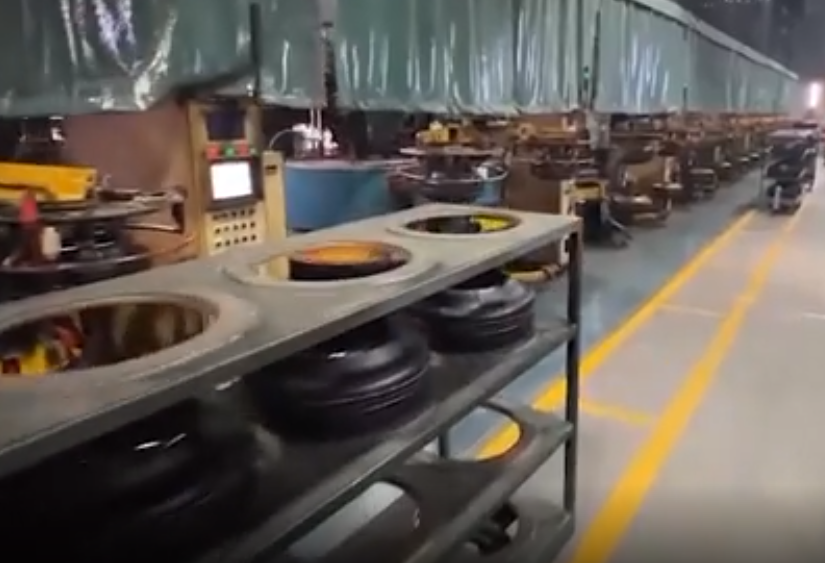
The Quality-Control Twist: Monitait's cameras were strategically placed to monitor each step of the production process, including the crucial curing stage. Here's where the real eye-opener happened. When the operators removed the tires from the curing press, they sometimes placed them on a separate tire trolley for later inspection. This practice, while seemingly innocuous, was the source of the problem.
The PLC counter, which determined tire production numbers, was checked by different operators across shifts. These operators, however, weren't fully aware of the product's quality, leading to inaccurate counts. This inaccurate data, in turn, influenced the company's raw material order estimations.
Monitait's Solution: Monitait's cameras didn't just capture visuals; they analyzed operator behavior during the tire removal process. They accurately counted the tires that were in good condition, excluding the defective ones from the count. This ensured precise production data and provided a comprehensive snapshot of tire exclusions for future reference.
The Power of Historical Data: By leveraging Monitait's historical data, the company achieved a remarkable feat. They could now estimate their tire orders with an astonishing 95% precision—5% more accurate than their previous methods. This precision led to significant savings in operator time and inventory costs, totaling approximately $200,000 annually.
In the world of manufacturing, even seemingly small inefficiencies can have significant consequences. For this company, Monitait proved to be a game-changer by shedding light on a subtle yet impactful problem in their production process. By harnessing the power of real-time monitoring and historical data analysis, they not only improved their inventory management but also ensured uninterrupted production. The lesson here is clear: when it comes to manufacturing, every detail matters, and the right technology can make all the difference.